January 11, 2024 Industry news
With a commitment to optimising operational efficiency and ensuring the highest standards of food safety, IPC recognise the importance of supply chain visibility.
In 2013 the business launched a new initiative to improve the quality of its product data with the ultimate goal of achieving end-to-end visibility — from supplier sites, through distribution centres, and on to consumer’s plates.
Their vision was to achieve full supply chain visibility to make real-time, fast, and accurate decisions while giving our customers what they demand.
The data challenge
Inconsistencies in product data was causing repeated disruptions to IPC’s supply chains, resulting in significant costs and risks to food safety.
Inaccurate weight and dimension data frequently led to incorrect freight calculations, resulting in overcharges, delays and unnecessary waste.
“We realised early on that we were never going to achieve end-to-end traceability and optimise our supply chain efficiencies if we didn’t use quality data,” said Lucelena Angarita, Director of Supply Chain Systems and Standards at IPC. “So, taking the time to lay this foundation was critical.”
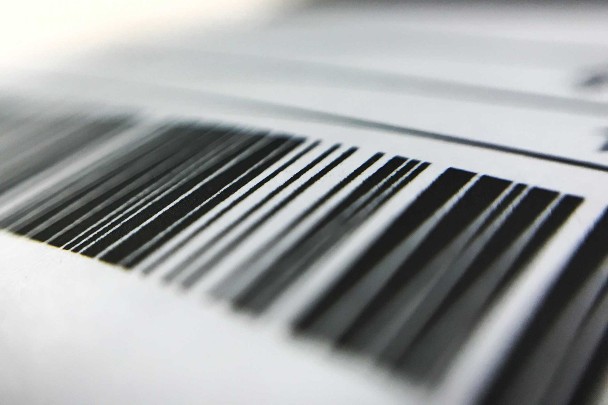
The first hurdle IPC had to overcome was getting all its suppliers and distributors to uniquely identify each of their products in the same way. IPC chose GS1 standards for this purpose, using Global Trade Item Numbers (GTINs) for product identification. IPC was then able to use the GS1 Global Data Synchronisation Network (GDSN) to share GTINs along with the relevant products attributes.
To ensure everyone was fully committed to delivering greater traceability, IPC engaged with stakeholders throughout their supply chains to ensure everyone fully understood the benefits of standardised identification and data sharing.
As a result, an impressive 99 per cent of IPC suppliers have since implemented GS1 standards, GTIN accuracy has reached 93 per cent of all products, and all suppliers and distributors are now consistently using the GDSN as “one source of truth” for the IPC system’s product data.
To track their progress, IPC scores their suppliers against two key metrics: data completeness and accuracy. Completeness is measured based on what percentage of the supplier’s products are published in the GDSN with complete “supply chain data” (product weights and dimensions) and “marketing data” (images, nutritional, allergens).
To ensure accuracy is maintained, Subway conducts periodic physical audits as part of its product evaluation process, weighing and measures specific product cases and comparing them to published GDSN data.
Part of the culture
Data sharing and end-to-end visibility are now at the heart of IPC’s culture. IPC continues to guide new suppliers on how to implement GS1 standards, engaging their technical teams, labelling staff, and other relevant teams to understand the requirements.
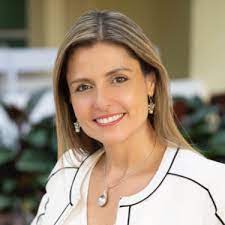
Quality data practices are now a part of our culture— within the IPC and with suppliers and distributors. We take time to recognise the efforts of our people and partners in instituting the use of standards. Using standards has become a natural way of doing business at IPC and Subway."
Lucelena Angarita
Director of supply chain systems and standards at IPC
IPC’s purchasing, distribution, and logistics teams have been particularly influential in driving the company’s adoption of GS1 standards to achieve full traceability. They in turn have been heavily supported by Subway’s Food Safety and Quality teams, acknowledging the difficulties and costs associated with recalls, have been strong advocates for standardised data.
Using data standards has become a natural way of doing business at IPC and Subway, who now require the use of GS1 standards in their supplier and distributor contracts. GS1 GTINs are mandated for all products and Global Location Number (GLN) are used to uniquely identify each physical locations where products are stored or manufactured.
New suppliers are typically given 90 days to comply with most of IPC’s requirements for data standardisation, a timescale most have been able to adhere to.
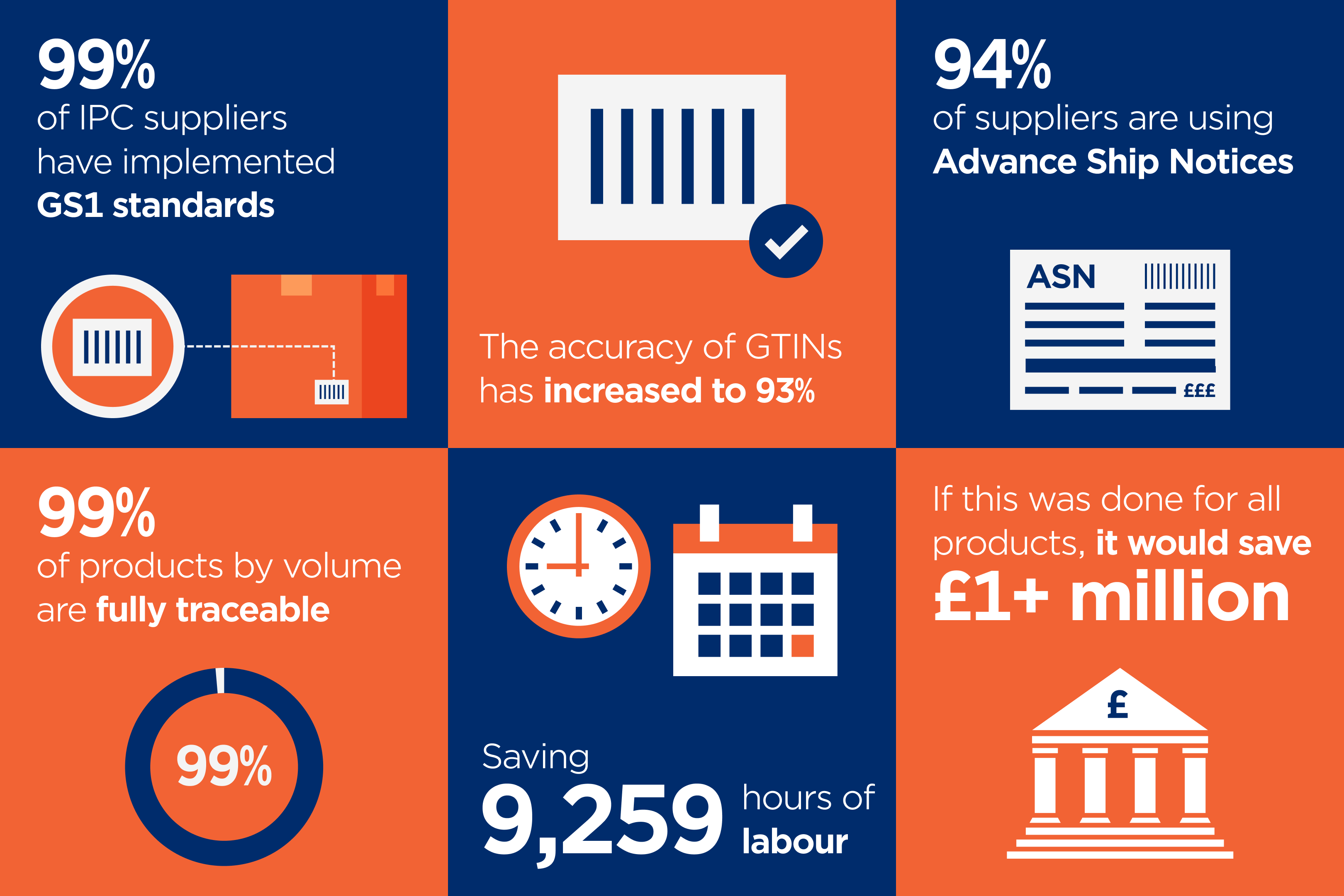
Results from the initiative
The benefits of traceability
IPC subsequently launched a traceability programme complete with milestones and targets for their supply chain partners. This included the encoding of GTINs, dates, and lots in GS1-128 barcodes for labeling and scanning packages and cases. They also began using GS1 Serial Shipping Container Codes (SSCCs) to identify products contained on pallets and now use GS1 standards in transaction documents such as invoices, inventory files and Advance Ship Notices (ASNs).
This has meant that suppliers now generate GS1-128 barcodes that provides Subway restaurants around the world a wealth of data for improving operational efficiencies and food safety. This includes real-time information on whether or not a product has a short shelf life, if it has been withdrawn or needs to be recalled.
All franchise owners are now equipped with a special app that allows them to scan GS1-128 barcodes to read or capture the GTIN, batch/lot number and expiration date of any product. This has enabled Subway to monitor freshness, track inventory and significantly increase the speed and effectiveness of product recalls.
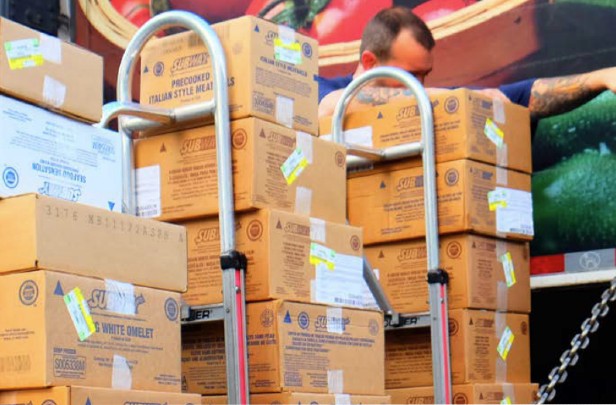
For distributors, the increased visibility this data enables has helped them become more efficient and precise when tracking and managing their inventory.
Overall, this has significantly reduced waste and therefor costs. IPC found that that correcting a one-and-a-half-pound weight differential on a simple jar of mayonnaise equated to a US $100,000 annual return-on-investment for the company.
As of 2021, the full impact of using quality data and the GDSN has been assessed at US $1.3 million in Subway’s annual in cost avoidance, clearly demonstrating the impact of inaccurate data on IPC’s bottom line.
Of course, the benefits of traceability are not purely financial and extend to all supply chain participants, from “farm to fork.” Suppliers only need to encode products once to supply hundreds of customers, distributors have greater inventory control, restaurant staff get alerts if they receive products outside of Subway Gold Standards’ shelf life, and consumers have greater assurance of safety and quality.